Want to Subscribe?
Read Corporate India and add to your Business Intelligence
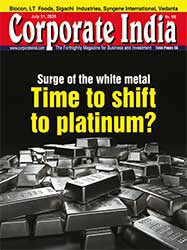
Unlock Unlimited Access
Published: December 15, 2024
Updated: December 15, 2024
Underlining its status as the second largest cement segment globally, the Indian industry has overcome a temporary blip in the first half of fiscal 2025 and is confidently meeting the domestic surge in demand with capacity additions as well as retail price hikes.
Earlier, there were production and consumption challenges on account of an extended monsoon, Lok Sabha and some state assembly elections, weak consumer sentiment influenced by an inflationary price spiral, and labour shortages.
But the industry is now back at the top of its game and all the indicators – demand, retail prices, and cement stocks – are back in the fast lane. Indicative of this resurgence are major cement stocks which have risen exponentially over the previous year, with analysts recommending these stocks even at the current sky-high levels.
Their enthusiasm is shared by Corporate India Research Bureau, which has highlighted five top cement shares for the consideration of retail investors, and five more scrips worth looking out for.
The $ 29 billion Indian cement industry, which churns out 391 million tonnes per annum as at present, and ranks as the second largest in the world, accounting for over 8 per cent of global installed capacity, is on a roll. December 2024 has emphasised the industry’s robust optimism. Earlier in the month, a price hike of Rs 10-30 per bag was implemented across the country, and a further price hike cannot be ruled out, considering the widespread demand for the commodity.
Little wonder, market prices of cement stocks have been scaling new peaks. Ultratech Cement, with a face value of Rs 10, which was available around Rs 6,600 a year ago, is in demand today at around Rs 11,764, while Shree Cement, also with a face value of Rs 10, which was available at Rs 21,433 over a year ago, is today quoted around Rs 27,925. Dalmia Cement, with a face value of Rs 2, which was available at Rs 575 a year ago, is quoted around Rs 1,876, while JK Cement (FV Rs 10), which was quoted around Rs 2,540 over a year ago, has buyers today at around Rs 4,617. And ACC (FV Rs 10), which was going abegging at Rs 84 two decades ago, is in demand today at around Rs 2,142. Interestingly, knowledgeable analysts recommend buying fundamentally strong cement stocks even at the current sky- high levels.
While the cement sector was ruling the roost in fiscal 2024, it has faced/is facing challenges in fiscal 2025 on account of the extended monsoon, elections for the Lok Sabha as well as over half a dozen state assemblies, and weak consumer sentiment influenced by an inflationary price spiral demand for cement.
The sector was also adversely affected by an acute labour shortage which led to a slowdown in construction work, which in turn cut demand for cement. But prospects ahead are highly promising and cement prices, demand for the commodity, and cement stocks are most likely to be buoyant going ahead.
With the drop in demand, cement prices during the first half of fiscal 2025 tended to seek lower levels, particularly in the southern and eastern regions of the country. On the other hand, the demand and prices of cement were more or less stable in the northern and western regions of the country.
The market sentiment and price trends have started changing in the beginning of the second half of 2025. Almost all cement producers have already jacked up prices by Rs 10 to Rs 30 per bag in different regions. Interestingly, the rising prices have not adversely affected demand and cement traders expect a further hike in prices going ahead.
The beginning of the second half (October 2024) also heralded the onset of the festival season. The sentiment in the cement sector was brightened on account of the return of labour, the rapid revival of construction work, receding monsoon disruptions and accelerating infrastructure projects. Renewed demand for homes led to a boom in construction of residential buildings.
Little wonder, cement companies started betting on these tailwinds coupled with potential price hikes, hoping for a fast recovery in operating margins. Needless to say, these companies are highly optimistic about a turnaround.
The cement industry is on a growth path. The industry's capacity is expected to expand at a CAGR of 4-5 per cent over the four-year period up to the end of 2027. It would thus begin the 2028 fiscal year with 715-725 mt/year in installed capacity. At present, the installed capacity of cement in India 600 mtpa with a production of 391 mtpa.
The industry is proceeding with expansion plans and capacity additions, despite dampened demand in the first half of 2025. Cement producers and industry observers foresee a modest 6-7 per cent volume growth this fiscal year, viewed in the context of expected demand revival in the second half. Though the sector witnessed a modest growth of 2-3 per cent in Q1FY25 due to a slowdown in construction during the Lok Sabha elections, there was a modest improvement in demand during Q2FY25. Well-known rating agency ICRA projects a 7-8 per cent growth for fiscal 2025, driven by strong demand in infrastructure and housing during Q3 and Q4. The country's demand for this year is projected to grow by 6-7 per cent.
Interestingly, during fiscal 2023, infrastructure had emerged as the top sector, attracting $ 11.6 billion across 57 deals, marking a 29 per cent yoy growth (as compared to $ 9 billion across 75 deals in 2022).
The cement industry was extremely happy at the Union budget for 2024-25. It noted that the government's strong emphasis on infrastructure development through various significant projects and allocations would undoubtedly drive demand for cement and other building materials.
Maintaining that "the announcement of Rs 11 lakh crore capital expenditure signifies the government's commitment to modernising India's infrastructure through various significant projects," Neeraj Alkhoury, CMA (Cement Manufacturers' Association) President, adds that "this will undoubtedly drive demand for cement."
It is undeniable that the infrastructure sector is crucial to the country's economic growth. The former British rulers had left India an under-developed country in 1947, in dire need of a comprehensive infrastructural base. After all, it is infrastructure which fosters the expansion of a variety of industries such as real estate and public utilities. A growing construction industry feeds off the rising needs for urban dwellings and powers the consumption of cement, thus boosting the Indian cement market.
With India's growing population and extensive infrastructural development, cement demand has been continuously on the rise. According to IBEF (India Brand Equity Foundation) statistics, this upward trend is projected to persist, with consumption expected to reach 600 million tonnes by 2025. The need for residential, commercial and industrial development drives this surge in demand.
Again, the construction of multimodal transport networks of world-class quality, including more than 100 Smart City projects, will further boost the cement industry.
Comments Mr Akhouri, "The government's commitment to ambitious projects such as the National Infrastructure Protection Plan (NIPP) and the Bharatmala road projects is leading to a substantial demand for cement." These initiatives aim to enhance the country's transportation network, including highways and roadways, necessitating large quantities of cement for construction. The Pradhan Mantri Awas Yojana (PMAY), with its urban and rural components, is a crucial driver for the Indian cement market. PMAY aims to provide affordable housing to all citizens, aligning with the government's vision of 'Housing for All'. The construction of millions of housing units under this scheme has led to a substantial demand for cement, particularly as the country is undergoing rapid urbanisation with an increasing percentage of the population migrating to urban areas.
According to projections, 39 per cent of India's population is expected to reside in urban areas by 2030, compared to the current level of 35 per cent. Urbanisation entails the construction of residential and commercial infrastructure, leading to a surge in demand for cement in various construction projects. The average size of the Indian household has been decreasing from 5.3 members in 2011 to 4.6 members in 2019, and this has gone further down to 3.6 in 2024. This shift towards smaller households is a noteworthy driver for the Indian cement market. Smaller houses result in the construction of more residential units to accommodate the growing population, translating into a consistent demand for cement.
The Indian cement industry has made rapid strides in size and stature in recent years, particularly after the shackles of controls were removed. Today, there is a total of 210 large cement plants, out of which 77 are in Andhra Pradesh, Rajasthan and Tamil Nadu. The installed capacity, which was around 390 million tonnes with actual production being 270 million tonnes in 2014-15, expanded to an installed capacity of 460 million tonnes in 2019- 20. The industry is expected to sustain its fastpaced growth and attain an installed capacity of 850 million tonnes by 2030 and 1,350 million tonnes by 2050.
Not just in size, the industry has made tremendous strides in technological upgradation and assimilation of the latest technology. At present, about 99 per cent of the total capacity in the industry is based on the modern and environmentally-friendly 'dry process' technology. Continuous modernization and technology upgradation with state-of-the-art technology is being pursued by the industry to achieve improved energy, environment and quality standards
Single production line capacity of over 12,000 t/d with multi-stream preheaters and calciners, average thermal energy consumption of 726 kcal/kg (3037 GJ/t) clinker or average electrical energy consumption of 78 kWh/t of cement, as at present, were unimaginable two decades ago, when these figures hovered around 3,000 t/d, 880 kcal/kg (3682 GJ/t) clinker and 120 kWh/t of cement respectively. The best levels of thermal and electrical energy consumption achieved by the industry, namely 686 kcal/kg (2870 GJ/t) clinker and 68 kWh/t cement, are comparable with the best in the world. Presently, cement companies in India are building global capacities, modernizing plants, improving efficiencies, cutting costs and restructuring their business houses to become highly competitive.
The technical innovations and constant modernization in mills, separators, calciners, burners, coolers, fans and air pollution control equipment have been chiefly responsible for such a phenomenal increase in capacity of single production lines as well as reduction in energy consumption and particulate emissions. The guide norms for cement plant operations developed by NCB (National Council for Cement and Building Materials) have also helped the industry in India to set up benchmarks for effective monitoring and improvement of operational efficiency.
The current fortunes of major players are worth recounting. Ultratech Cement, originally created by engineering colossus Larsen & Toubro and subsequently acquired by Kumar Mangalam Birla of the Aditya Birla group, whose shares have a face value of Rs 10, crossed a historic milestone of Rs 10,000 to reach Rs 12,144 before settling at around Rs 11,760. Ramco Cements, which had gone up to Rs 636 (FV Re 1) last year, has shot up further to Rs 1,058 before reacting to Rs 941. ACC, which was friendless in 2000 at around Rs 84 and had climbed to Rs 2,843 early last year, has settled around Rs 1,875. Ambuja Cement, which was going abegging around Rs 93 in 2008, shot up to Rs 315 early last year and has now spurted to Rs 525. JK Cement, which had no takers at around Rs 35, skyrocketed to Rs 4,896 this year before settling around Rs 4,615 at present. Dalmia Bharat, with a face value of Rs 2, which was quoted around Rs 406 in 2020 and climbed to Rs 2,429 earlier this year, is now placed around Rs 1,876. RHI Magnista India, formerly known as Orient Refractories, with a face value of Re 1, surged from Rs 576 early last year to Rs 870 before quoting around Rs 728.
Interestingly, almost all cement stocks are currently quoted at sky-high levels and continue to attract inquiries and demand from investors.
In this scenario, discerning investors will do well to include fundamentally strong cement shares in their portfolio. There are several prime cement stocks which are worth investing in. Corporate India Research Bureau has selected top five shares which are doing well and are expected to fare better going ahead. Besides, it has suggested five more scrips which can be placed on investors' radar. Happy investing!
Ultratech Cement, belonging to the Aditya Birla grouop, the largest cement manufacturing company in the country, and the third largest in the world (outside China), is a $ 70 billion building solutions powerhouse. It is also one of the leading players in the white cement segment in India. The company's business operations span the UAE, Bahrain, Sri Lanka and India.
With 23 integrated manufacturing plants, 29 grinding units, one clinkerisation unit and 8 bulk packaging terminals, Ultratech is the only cement company in the world (outside China) with 100+ mtpa of cement manufacturing capacity. In order to move towards achieving its target of 200 mtpa capacity, the company has acquired the cement business of Kesoram Industries.
The company's building products business is an innovation hub that offers an array of scientifically engineered products to cater to new-age constructions.
The company has gone from strength to strength on the financial front. During the last 13 years, its sales turnover has more than trebled from Rs 18,351 crore in fiscal 2012 to Rs 70,903 crore in fiscal 2024, with operating profit moving up from Rs 4,194 crore to Rs 12,760 crore and the profit at net level inching up from Rs 2,389 crore to Rs 7,004 crore. Ultratech's financial position is extremely sound, with reserves at the end of March 2023 standing at Rs 59,939 crore - over 207 times its equity capital of Rs 289 crore.
The Ultratech stock is a favourite of research analysts, institutional investors and high net worth investors. The Rs 10 face value stock had climbed Himalayan heights of Rs 12,144 before settling around Rs 11,764. Prospects for the company are robust going ahead.
The Bangur group-owned Shree Cement is one of the two leading cement groups in India with a cement production capacity of 50.4 mtpa and a power generation capacity of 771 MW. Since its inception in 1979, the company has been on a sustainable and inclusive growth path with its consistent pursuit of innovation and operational excellence.
Since inception, the company has grown steadily to emerge as one of the top cement companies in the country and one of India's most cost-efficient cement producers.
Shree Cement's Navalgarh cement plant has gone on stream. According to Dow Jones, the plant has an integrated cement capacity of 4.2 million tonnes per year. The company has accelerated its growth plans and outlined expansion plans of 12 mtpa at a capex of Rs 70 billion. This, along with the ongoing plans will increase the company's capacity to 72.4 mtpa. It plans to achieve a capacity of 80 mtpa in the next few years.
The company has been performing very well on the financial front. During the last 12 years, its sales turnover has trebled from Rs 5,641 crore in fiscal 2012 to Rs 20,521 crore in fiscal 2024, with operating profit inching up from Rs 1,646 crore to Rs 4,518 crore and the profit at net level more than trebling from Rs 618 crore to Rs 2,396 crore. The company's financial position is very strong, with reserves at the end of March 2024 standing at Rs 29,843 crore - over 578 times its equity capital of Rs 36 crore.
The company's stock is the most expensive cement scrip in the country. The share with a face value of Rs 10 is quoted around Rs 27,926. This can be a good addition to the portfolio of investors with a long-term perspective.
Over eight decades old, Dalmia Bharat is among the top five cement companies in the country with a strong presence in 22 states, serving clients through an extensive network. It has a total capacity of 35 million tonnes per annum, with its current capacity mix spread at 59 per cent in the east, 33 per cent in the south and 8 per cent in the west.
The company is growing steadily in its financial performance. During the last 12 years, its sales turnovalmost doubled from Rs 7,444 crore in fiscal 2012 to Rs 14,691 crore in fiscal 2024, with operating profit moving up from Rs 1,894 crore to Rs 2,684 crore and the net profit shooting up two and a half times from Rs 44 crore to Rs 853 crore. The company's financial position is very strong, with reserves at the end of March 2024 standing at Rs 15,359 crore -- over 400 times its equity capital of Rs 38 crore.
With a view to expanding its size and stature, the company has now decided to acquire Jaypee Cement, a part of Jaiprakash Associates. The deal's cash outflow is earmarked at around Rs 3,300 crore. According to the deal, which is slated to be completed by March 2024, Dalmia Bharat will acquire Jaypee's plants situated in UttarPradesh, Madhya Pradesh and Chhattisgarh at a total cost of Rs 5,500 crore.
The acquisition is expected to give Dalmia Bharat a strong foothold in central India, which accounts for 15 per cent of the country's cement demand. Again, Dalmia Bharat's capacity will be now more diversified with 52 per cent in the east, 26 per cent in the south, 16 per cent in the central India and 6 per cent in the west.
In the current boom period, the stock price of Dalmia Bharat has shot up from the 52-week low of Rs 575 (face value Rs 2) to Rs 2,429 before settling around Rs 1,876. The acquisition of Jaypee Cement is expected to brighten the prospects of the company going ahead.
Starting with a small plant in Nimbahera, situated in Chittorgarh district of Rajasthan, with a capacity of 3 lakh tonnes per annum in 1975, JK Cement, belonging to the well-known industrial JK group, has emerged today as a leading cement company producing high-quality cement with several plants located at Golan (Rajasthan), Muddapur (Mudhol taluk in Bagalkot district of Karnataka), Jhajjar (Haryana), Aligarh (UP), Balasinor (Gujarat), Katni (Madhya Pradesh), Ranna (Madhya Pradesh), Aamirpur (Uttar Pradesh) and Fujiara (the Middle East), among others. The company was the first to produce white cement in the country.
The company is known for the high quality of its cement. At its Golan white cement plant, it uses the technical expertise of FL Smidh & Co from Denmark and state-of-theart technology with continuous on-line quality control by micro-processors and x-rays to ensure that only the purest white cement is produced. The company manufactures white Portland cement through 5 significant stages -- crushing, raw meal grinding, clinkerisation, cement grinding mill, and crushed limestone. Clays and feldspar are fed through electronic weigh feeders.
The company has done very well on the performance front. During the last 12 years, its sales turnover has expanded by around four times from Rs 2,545 crore in fiscal 2012 to Rs 11,566 crore in fiscal 2024, with operating profit shooting up from Rs 514 crore to Rs 2,071 crore and the profit at net level spurting from Rs 175 crore to Rs 290 crore.
In the current boom period for the cement industry, the stock price of JK Cement has advanced from the 52- week low of Rs 2,542 to Rs 4,896 before settling around Rs 4,615. Prospects going forward are quite promising. Discerning investors can certainly accumulate this stock at every decline.
Established in 1936, ACC (Associated Cement Companies) is one of the oldest cement companies in the country and is synonymous with cement. Originally belonging to the Tatas who sold it to the Holcim group of Switzerland, it was acquired by the Ahmedabad-based Adani group in 2022. The company produces a wide range of cement products and has demonstrated consistent financial growth.
During the last 13 years, the company's sales turnover has almost doubled from Rs 10,153 crore to Rs 19,460 crore in fiscal 2024, with operating profit inching up from Rs 1,921 crore to Rs 2,059 crore and the net profit moving up from Rs 1,301 crore to Rs 2,337 crore.
Future prospects for the company are all the more promising. According to the management, "Going ahead, cement demand in India will continue to grow at 7-8 per cent, primarily fuelled by investments in infrastructure and large-scale residential housing projects."
As a result, ACC shares shot up to hit a 52-week high of Rs 2,543 before settling around Rs 2,142. As these shares have entered a bullish mode, future prospects are quite healthy.
Besides these five strong cement stocks for investment we suggest following five stocks to keep on your investment radar.
July 31, 2025 - Combined Issue
Industry Review
Want to Subscribe?
Read Corporate India and add to your Business Intelligence
Unlock Unlimited Access
Lighter Vein
Popular Stories
Archives